SAVVY® was honored with third place at this year’s Swiss Logistics Award Night. The solution: The “Smart Bogie” collects numerous data in real time during the journey via measuring sensors attached to the freight wagon. This data is evaluated intelligently and centrally using various algorithms. In case of anomalies in corresponding indicators, the system informs the relevant stakeholders if action is required.
The Swiss Logistics Award is organized by GS1 Switzerland. It is a prestigious award in the logistics industry that recognizes Swiss companies for their outstanding achievements and innovations in logistics.
The event and glamorous and inspiring night took place in Bern, where leading minds from the logistics industry came together to celebrate the latest developments and successes.
The selection and presentation of the 29th Swiss Logistics Award is carried out by the jury appointed by the GS1 Switzerland Board. It consists of experts and neutral representatives with a high level of expertise in related industry.
About SAVVY® Telematic Systems AG
SAVVY® Telematic Systems AG (www.savvy-telematics.com), headquartered in Schaffhausen, Switzerland, is a leader in innovative telematics, sensor and software solutions that make an important contribution to digitisation in the chemical and logistics sectors. The objective is to increase added value in these companies by means of efficient work and logistics processes. SAVVY® combines high-tech telematics system solutions for use in rail freight wagons, (tank) containers, IBCs, vehicles or machines with sophisticated telematics technology and a process-oriented state-of-the-art portal. The range of products and services also includes extensive process consulting and intelligent process design for all telematics and sensor-based as well as digitising business processes in chemical, industrial and logistics companies.
As of May 2014, SAVVY® is a second-tier subsidiary of the SDAX-listed INDUS Holding Group (www.indus.de). The resulting financial stability is unique on the market and ensures SAVVY® customers’ investments are protected and absolute data management neutrality maintained.
Press contact of SAVVY® Telematic Systems AG
Aida Kaeser
Co-Founder & CEO
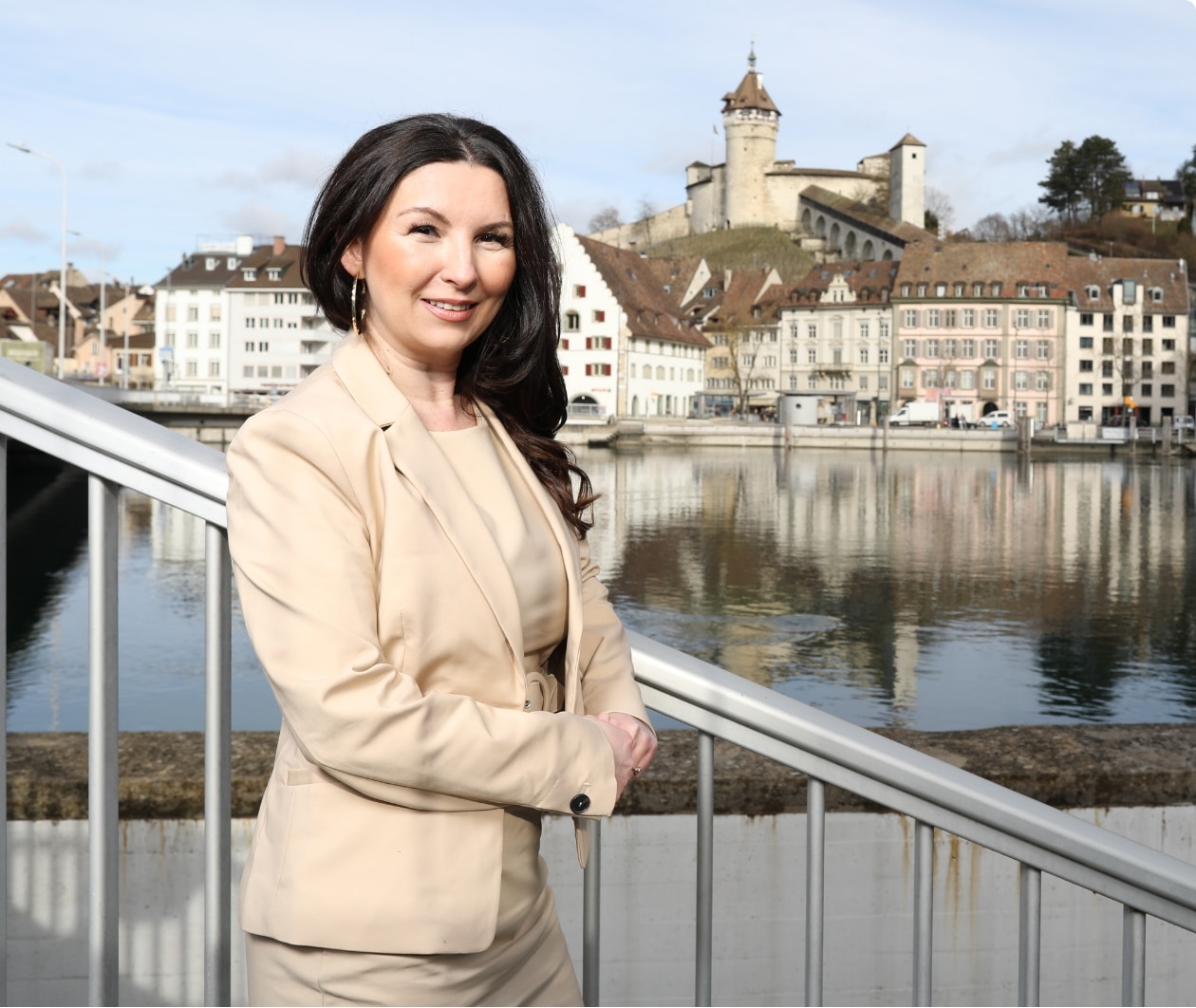